Stereo Mojo – Sistrum Component Rack
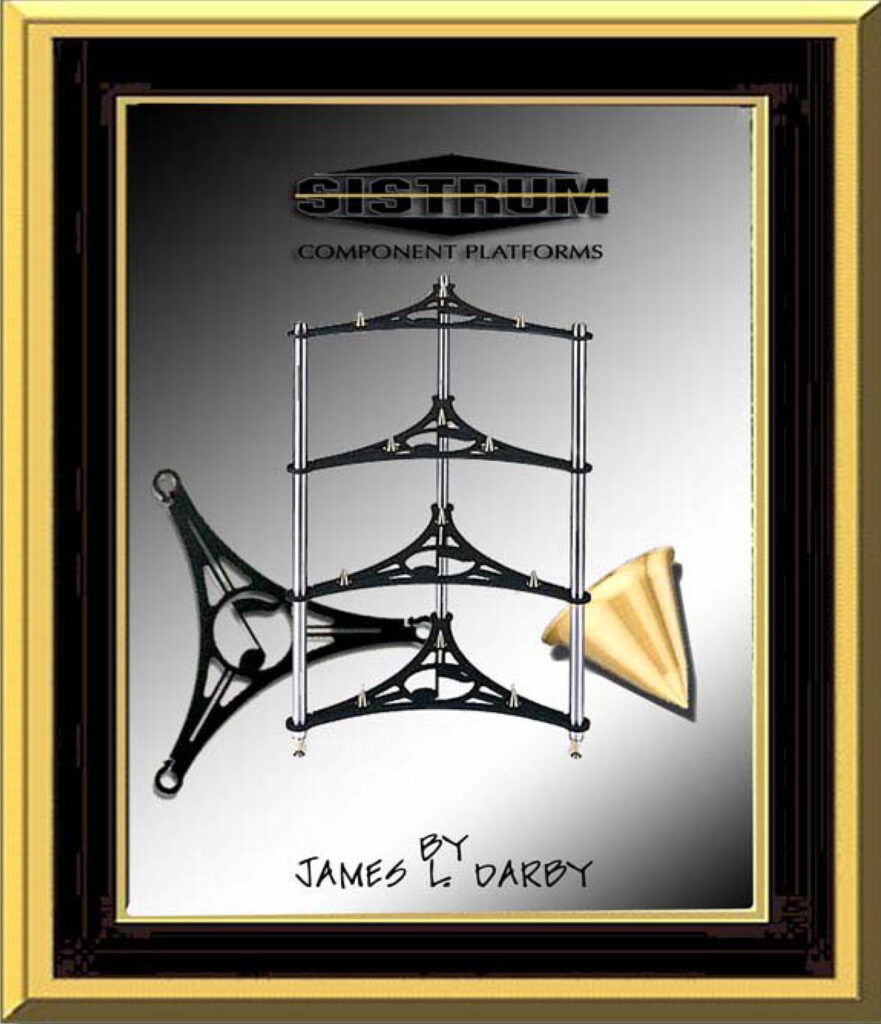
Price: $2249.99
Skep·tic [skep-tik] – noun
- a person who questions the validity or authenticity of something purporting to be factual.
A good audio reviewer should, I think, possess a healthy amount of skepticism when it comes to claims made by audio manufacturers. You have seen them. Speakers that claim to be the best in the world. Period.
Cable makers that claim their cables are simply magical. While I am not a native of the state of Missouri, their “Show me” motto has a certain validity in a world where ultra-hype is the name of the game. No area of high-endism seems more prone to outlandish hyperbole than that of accessories and/or tweeks – those devices that do not reproduce sound on their own but profess to improve it by employing them.
The key word in the above definition is “questions”. A good reviewer’s skepticism must never cross the boundary into bias. In short, question but be open minded and ready to admit when your doubts are proven baseless.
When Robert Maicks of Star Sound Technologies asked me to review his Sistrum audio component platforms (component shelves, racks), I was concerned. I had read many reviews over the years describing the “sound” of different shelves – usually very expensive shelves – that ascribed audio qualities akin to any other amplifier or speakers. I read the descriptions in several audio catalogues that made promises of drastic improvements. I was dubious. What’s more, I confess I was little fearful that I would not be able to hear that much difference in a review setting. After all, I had purchased and used inexpensive audio- specific racks over the years with spikes and rigid construction and all they did was hold my audio stuff.
But, the one thing of which I was certain is that no matter what, whether it embarrassed me by exposing some shortcoming in my audio sensibilities or not, I would report the truth of my experience.
THE DEVIL IS IN THE…
…Details. As usual, I asked the designer what the design goal for the Sistrum system was. His reply is one of the most specific and detailed in Mojo history;
“Establish a newfound approach to vibration management with a primary focus on hi-fi components and loudspeaker systems. Understanding vibration, along with the negative effects caused from vibration, is a compelling new study in the scientific community. There are many markets of choice, like the hi-fi market, that companies can participate in.
To provide a highly mechanical yet easily understood methodology that is focused not only on the rapid dissipation of resonant energy which forms chassis surface of electronic components and loudspeakers, but that also concentrates on dissipating vibration that affects even the smallest of surface mount parts such as resistors, transistors and circuit boards. One could identify it as a micro-resonance management process. These studies and experiments led to the discovery of our Live-Vibe Technology™ – The Science of Resonance Transfer. We state that “If a chassis is going to vibrate – let it” as the resonance transfer process always leaves the equipment and energy in a constant state of motion – always vibrating. We do not inhibit or try to stop vibration as vibration itself carries all of the dynamic properties and harmonic layers that we are listening for.
The focus is to rapidly transfer resonant energy impeded by the effects of Coulomb friction which is caused by lack of mechanical conductance between two surfaces (over damping). This friction creates inefficiencies within mechanical, electromechanical and acoustic chassis and within all parts thereof.
Our overall goal is to continue to improve the enjoyment we get from listening to recorded music and enhancing, dramatically, the always elusive “sound of the live performance” within the confines of our homes, theaters, and listening rooms”.
Mr. Maicks sent a four shelf (or, as he calls them, platforms) rack. Various sizes are available, but at four feet tall, assembly was not difficult, aided by a good set of instructions.
There are three main support rods that weigh about 12 lbs. each. Each rod incorporates three separate design elements. First there is a stainless steel hollow tube. The second part of the support features a solid half-inch diameter brass threaded rod positioned in the center that runs the length of the tube. This rod threads into the top and bottom end cap thus producing the mechanical seal that holds the fill material in place. It also comes in contact with the brass Turning Bolt thread located at the top and the brass Audio Point thread located at the base of the rod. These three brass internal parts joined are known as the primary conductor. The third item is the Micro-Bearing Steel fill material which contacts the stainless steel tube with the primary conductor. This joining, says Robert, continuously moves energy at a consistent speed without sinking the dynamic signature that the platform provides. These rods are assembled at the factory, including the Micro-Bearing Steel fill.
A lot of time and testing went into the development of the support rods as Robert explains; “In the development of the support rods we were faced with a few challenges whereas we did not want to sink the dynamic or over-damp the signal. First we employed a solid stainless rod and the sonic result was negative. The second concept was to use a stainless tube and fill the tube with a conductive material as we chose to use iron ore. The ore began to bring the design to life – then we realized that iron ore rusts in humidity. The next choice was a slag steel aggregate which was chips of varying shapes and sizes which worked, but not to the extent of the iron ore. We later moved onto the concept of a single stainless steel rod placed down the center of the tube surrounded by the slag. The design began to function at a much higher level of efficiency. After spending more time in testing the result ended up employing a brass threaded rod for speed down the center of the tube and finally discovered that steel ball bearings the size of BB’s provided an even grain structure that moved more energy and at a higher rate of speed. We then began reducing the size of the bearings on to powder form where the performance absolutely died. We then increased the sizing to what we found to be the optimal size.
Thus a high-speed conductive pathway was formed employing three materials combined to match a frequency bandwidth that simply worked”.
The micro BB’s, thankfully, are also pre-filled into the support rods at the factory. Tiny ball bearings, if spilled into a carpet, would most likely destroy a vacuum cleaner and spilling them on a bare floor would turn it into an ice rink.
Robert also stressed the importance of using “cold rolled steel” in the design mechanism. “There are different processes used in the manufacturing of steel. When steel is manufactured via a “hot process” a high percentage of lead is used in order to provide a lower cost steel. Hot rolled steel is steel that is rolled to size in the mill while red hot. Hot rolling steel does not harden the material as much as cold rolling will. The majority of these lower grades of steel contain tremendous amounts of lead and zinc.
The “cold rolled manufacturing process” traditionally named as “white steel” is a type of steel product which is produced by a cold rolling process (without heat), and has typical properties which significantly differ from Hot Rolled Steel (HRS) or “black steel”. CRS has better surface quality, thinner and more precise gauges. Cold rolled steel employs greater percentages of the higher quality elements and much less zinc and lead thus establishing a much higher grade of steel”.
GET THE LEAD OUT
“Lead is not our favorite choice of materials for equipment used in the music, instrument and sound reproduction businesses”, Robet explained. “Lead is a primary absorbent material that absorbs all energy and is very difficult when employing a specific geometry such as the science of resonance energy transfer. In general, softer steel composites and material with surface or internal deformations and flaws will not transmit resonant energy as well. Vibration consists of many properties, two of which are the dynamic and harmonic structure of sound. As audiophiles we strive to retain those properties and do away with others caused by Coulomb Friction which is formed from the impendence of vibration. Coulomb’s friction establishes inefficiencies along mechanical, electromechanical and acoustic signal pathways thus will limit the performance of the musical reproduction system.
Brass also has similar characteristics and levels of manufacturing grades of quality (lead included) as well. The $300 saxophone does not use the same grade of brass as the Selmer MK-VI selling at $5,000 as the acoustic properties of brass change dramatically depending on the amount of lead formulated in the mix. A sound reproduction system can loose its ‘live dynamic’ simply by employing too much material including the higher grades or the wrong choice of material such as lead. Material science is as important to the function of the design as the application of geometry”.
THE PLATFORMS
Whew. That’s a lot of technology buried in something that looks to the observer like a simple steel rod! I should note that Audio Points are also attached to the bottom of the three supports for a solid grouding with carpeted floors.
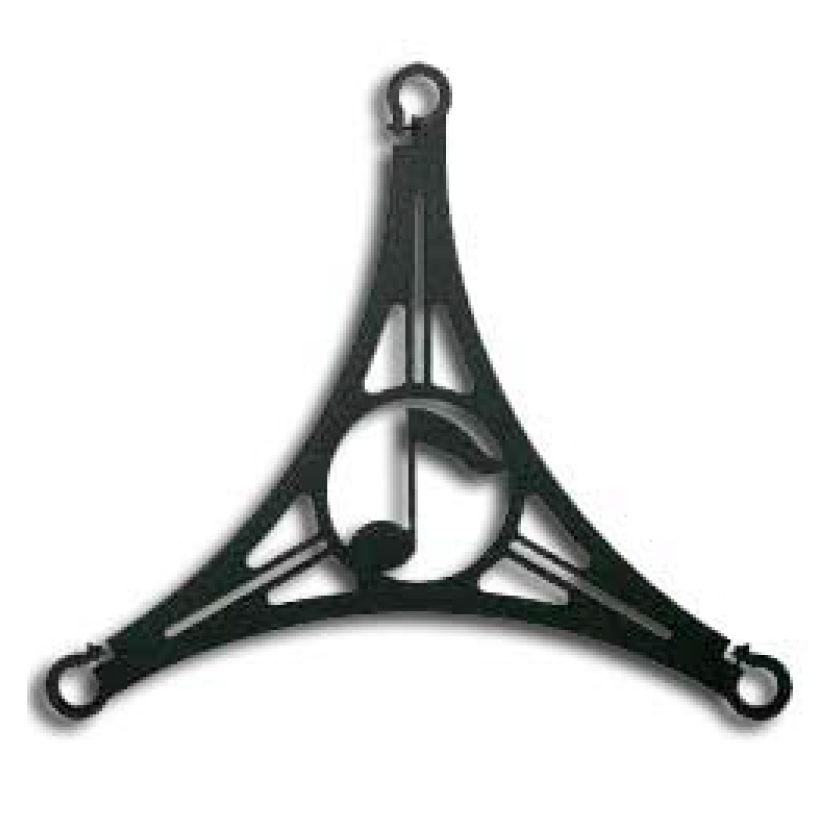
Attached to the three high-tech poles are the black shelves, oops, platforms. They are designed, apparently, to maximize strength (each one is capable of holding 300 lbs.) and minimize mass and resonance. In the center of each is formed a musical note – an eighth note to be precise – as a little art as part of function. Nice touch. As you can see, the platforms slides down over the rods and are secured by tightening via the included Allen wrench. Though the shelves are pretty much self leveling, I used a level to make sure they were perfect. The effect of tightening the Allens was to clamp the platforms solidly via steel-on-steel contact. In the time I’ve had them, many different components have been slogged in and out with a ton of adjustments. There has never been any slippage or metal
fatigue. The platforms do inspire a great deal of confidence.
GETTING TO THE POINTS
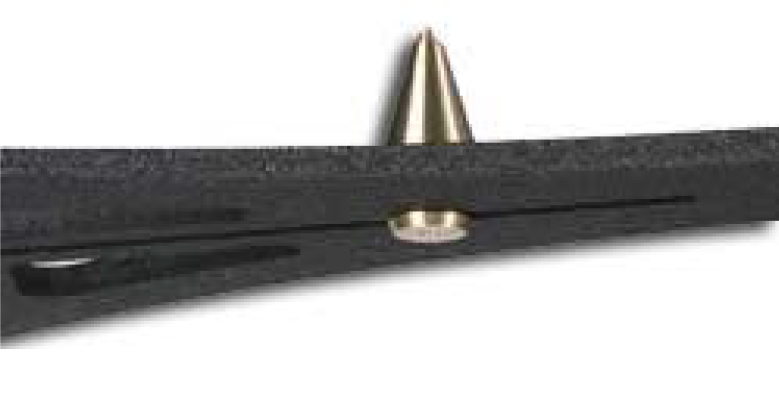
Included in the system are three inverted, pointed cones called Audio Points. You install them in the three provided channels and lock them down by a simple twist or two. The channels are long enough so that a proper adjustment should support any component. The next part can be a little tricky, but having accomplished it would not have to be repeated until you change or move something. Also provided are small brass disks (APCD2 Coupling Discs) that are flat on one side, the side that contacts your boxes, and the other side dimpled in the center to accommodate the sharp point of the inverted cones.
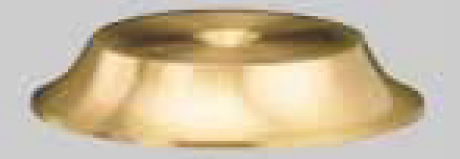
The trick is to get the dimples and the points to match up beneath your components. It’s like juggling dinner plates on a broom handle. The manual suggests that a piece of tape be used to secure the disks to the points, which works fine. The only problem I encountered is with something as light as the Oppo universal player; it tends to slip when you go to push a button, say to open the disc drawer. Other than that, the Sistrum system has been home to my 80 lb. LSA integrated amp, Richard Dolan Monoblocks as well as a host of other disk players, power amps, preamps, DACs and even turntables.

NICE RACK
When I got everything mounted and fired up the system, my iron-clad skepticism vanished. Poof! I had been expecting maybe a slight difference if I listened real close. The sound of the system was not just improved, it was transformed! I was stunned. The effect was not at all subtle, but was so obvious that my wife came running in when she got home and asked what had made such a big difference. She had heard it from the other end of the house without even critically listening.
The question is not so much what improved, rather it is what did NOT improve, to which I would say – nothing. Everything was better. The noise floor was reduced considerably, leaving room for greater dynamics and more detail. Everything sounded faster. Transient attacks, instrument plucks and strikes and even the bass was more rhythmic and clean. Solo vocals were more rounded and fleshy and stood out a little further from the accompaniments. I can’t say the soundstage was dramatically wider or deeper, but the layers within the stage, especially on orchestra recordings, were more defined and easily heard.
The character of the recordings were not changed, although at first a bit of extra brightness was perceived. But the more we listened, it was not brightness at all, just the clarity of everything we heard.
As to appearance, I must say that seeing my components isolated and seemingly floating in air is very cool. The minimal visual impact of the system does not detract from the look of your components – in fact, it rather showcases them. It does not look like a piece of furniture, which can either be good or bad
depending on your tastes.
THE DOWNSIDES
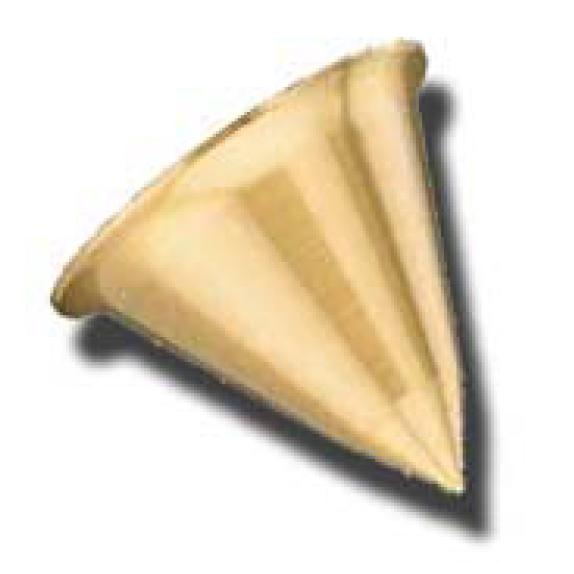
There are three points of which you need to be aware that could figure into whether this product is for you or not. First, there is no inherent cable management system built into the Sistrum. No channels or conduits that let you hide your IC’s, speaker or power cables for a clean, professional appearance. One solution is to simply use twist-ties or other simple fasteners to strap the cables to one or more of the vertical columns and run them to the floor or between shelves. For most audiophiles, this is not problem. But, if you change components or move them frequently like a reviewer must, this can be a bit of a hassle.
Second, if you have a component that is very lightweight such as the Oppo disk player, it may be prone to slide every time you push a button. Or, if you attach heavy IC’s or power cables to the component, it may not stay in place at all. Perhaps using a bit of something like BlueTak atop the discs will solve that hitch as well.
“The sound of the system was not just improved, it was transformed!
STEREO MOJO
I was stunned!”
Third, and perhaps most importantly, because of the design that demands that you place a
component on the “points” and there is but one set of points per shelf, useable horizontal space on each shelf is limited, particularly since the concave curvature of the triangular shelves have practically no surface. One would have to stack components on top of each other if need be, but you couldn’t set a small phono pre, for instance, next to a preamp on the same shelf. If you have a tube amp where the tubes are exposed, you won’t be placing anything on top of that. And stacking some boxes will cause heat dissipation problems. There is not really a flat surface on the platforms, such as you would find on a Stillpoints or Finite Element (reviewed earlier) where one might want to set a record cleaning brush or the case to the CD your playing for example.
A DIFFERENT APPROACH
You have probably seen in publications such as Stereophile and TAS where the reviewer points out some perceived deficiencies in a product. Then, in the very back pages, the supplier is given an opportunity to respond. It may be in the same issue or it could be published a month or two later. Stereomojo takes a different approach – we let the supplier know before we publish the review so that he can repond within the review itself without making our readers wait until later or force them to find them where they are buried somewhere else.
In this case, Robert was informed of the above criticisms and responded to them point by point as follows:
Point one – Cable Management:
“When any product comes in contact with Sistrum, a change in the overall performance quality of sound is inevitable – including most cable designs. Star Sound has spent the past three years designing a cable management product named the Cable Chase Network™ that attaches to the rear support rod of the Sistrum Platform. Similar to the design of the APCD2 Coupling Disc we are attempting to manufacture a product that remains neutral in sonic or improves upon the sound of the system. When cables come in contact with the Sistrum Platform a mechanically grounding of the cable too takes place. This grounding usually changes the sonic of the cable or system due to the functional design of the platform.
When wood, acrylics or composite racking materials come in contact with cables it too can change the sonic as the vibrations from these materials will add additional frequencies to the energy running along and through the cable.
Our approach to understanding cable design is that we do not wish cables to come in contact with each other a,s depending on the cable design, this too can have an ill effect on the quality of sound so we do not recommend grouping cables together.
Sistrum is an extremely efficient vibrating grounding plane and our knowledge is that if a system shares the same acoustic, mechanical and electromechanical ground the less interrupted signal flow provides a higher level of efficiency and that leads to a greater level of listening enjoyment. Again the problem lies in the geometry of the design as not to over-damp or disrupt the signal pathways. It is our intent to close the book on this design later this year as we are confident in the fact that the Cable Chase Network provides many more pros versus cons related to cable function”.
Point two – Small Chassis Equipment:
“Small chassis (or very lightweight – publisher) products where extremely rare if any existed at all when Sistrum was first introduced as we are currently witnessing the evolution or how trends impact the manufacturing of equipment platforms and technology. We work with listeners on an individual basis should they require assistance in positioning products onto our shelving. We provide additional pieces of steel for placement, additional Audio Points and supportive measures that function should chassis size become an issue. We highly recommend clients to contact us prior to employing other materials such as Blue Tak as this material will cause Sistrum performance to deteriorate. We will always be happy to answer all of your questions.
Point three – Stacking Components and Placement of Accessories:
“In some cases where listeners preferred to stack equipment on a single shelf we recommend the smaller .2AP.7D non-threaded Audio Points and the APCD2 Coupling Discs placed between the chassis forming a metal to brass to metal contact. This mechanical coupling of the components chassis now vibrate as a single mass thus permitting the shelf to pass the energy to the support rods maintaining speed and efficiency. For absolute best results we recommend one chassis per shelf.
With regards to placement of accessories such as a record cleaning brush, etc we manufacture an extra large top shelf that mounts into the top of the three support rods. Simply remove the existing top brass bolts, place the shelf and screw the bolts back in securing the shelf to the platform. The shelf is large enough to handle the largest of turntables leaving some room for accessories. In some cases and depending on the sensitivity of the system accessory items can also alter or influence the sonic
performance”.
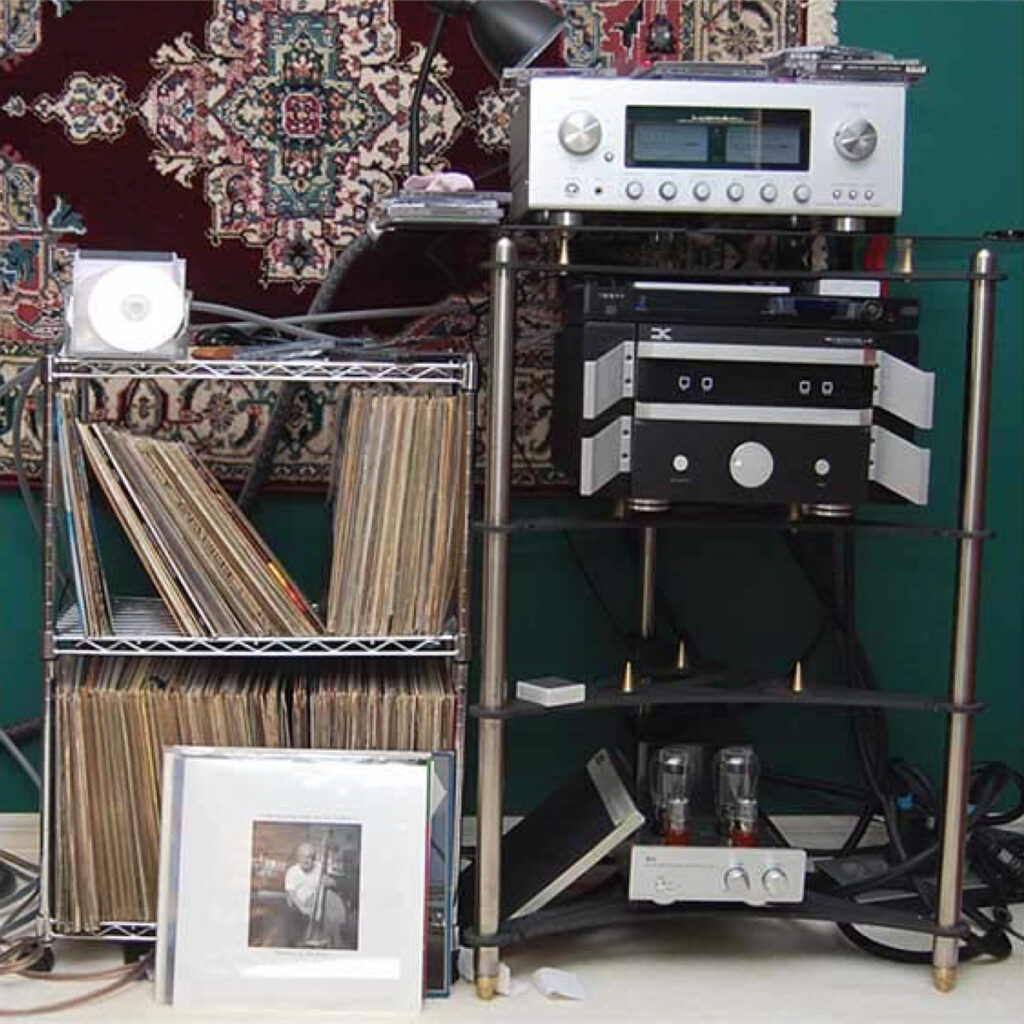
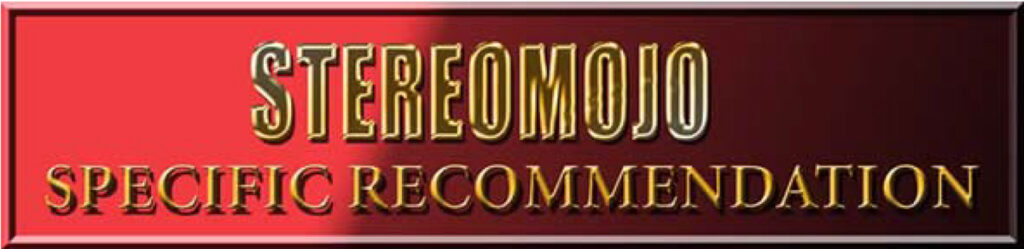
For me, the Sistrum rack proves that how and where you house your components matters. It also
indicates that there is probably a lot of performance lying hidden in your system just waiting to leap out.
The Sistrum lets ‘em leap. From a cost standpoint, there are many racks that cost much, much more. Are they better and worth the additional investment? That I can’t say – yet. All I can say is that it appears, within the limitations identified, that the Sistrum system is a good value and performs exactly as claimed.
As for me personally, I do not even want to think about replacing mine. If you have a significant investment in your components and do not have a system such as this, you should definitely try it.
Sistrum does have a policy in place and a guarantee that lets you do just that. You should read the details here.
Stereo Mojo